
全面生產?維護TP?M培訓公開課咨詢課?程—歡迎企業內部培訓和培訓機構合作垂詢
護TP?M培訓公開課-培訓地點:江蘇無錫萬達廣場 每月開班 小班教學、滿四人開班
金舟軍老師 手機/微信:13816949004 QQ郵箱:923503608@qq.com
以應用為導向的全面生產維護TPM咨詢培訓,學員培訓后就會應用全面生產維護TPM,金舟軍老師通過嚴格的培訓流程確保顧客滿意
請點擊查看—金舟軍質量管理工具培訓咨詢實施流程
全面生產維護TPM培訓講師質量專家金舟軍,全面生產維護TPM培訓咨詢機構上海科租企業管理咨詢有限公司,是專業、實戰、解決實際問題的培訓全面生產維護TPM培訓包括TPM實戰案例、設備FMEA在TPM中的應用,TS內審員公開課和企業內訓請垂詢培訓大綱,TPM培訓資料光盤贈送
最有價值的全面生產維護TPM培訓公司
上海科租企業管理咨詢有限公司金舟軍老師自辦全面生產維護TPM培訓咨詢公司,培訓老師自辦咨詢公司省出了業務費用和老板利潤,客戶的培訓費全部變為培訓老師的培訓費,能為客戶提供優質服務,客戶培訓價值最大化值 。只要學員參加過質量培訓課程,將為學員提供終生的培訓課程答疑。
最具專業的全面生產維護TPM培訓講師
金舟軍二十多年專業從事全面生產維護TPM培訓講師,專業涉及質量管理和精益生產課程,客戶涉及世界五百強企業, 每個培訓項目的客戶都有培訓現場的視頻和照片為證。金舟軍老師課程以應用為導向,課堂上只講干貨,絕不以無關的游戲打發時間。
培訓的客戶-全部有客戶培訓現場照片、視頻為證!

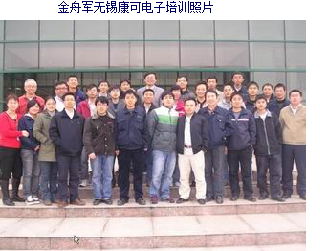
金舟軍老師TPM培?訓優勢

重慶長安汽車、上海延鋒韋世通、上海NEC、上海德爾福、武漢東風汽車、江蘇東風起亞、江蘇麥格納、安徽康佳電器、、安徽博西華、上海奧托立夫、浙江海信惠爾浦、沈陽寶馬汽車、上海大金空調、遼寧大連固特異輪胎、長春大眾集團、湖北武漢佛吉亞、上汽集團、吉林一汽集團、廣西上汽通用五菱、廣西玉林重工、江西長力股份 北京北汽福田、深圳中興通迅、福建新能源科技、湖南三一重工、蘇州恩斯克軸承、河北天威光伏、武漢哈金森、蘇州力特奧維斯、重慶 嘉陵集團 福建奔馳汽車、遼寧大連大眾變速箱 廣東廣州京信通信、深圳中興通訊 河南利達光電 河南新鄉豫新 河北萊尼、山東萊尼 、山東勝地、陜西中航、湖南時代電氣、天津中核
全面生產維?護T?PM培訓課程公開課視頻金舟軍老師好看視?頻主頁
全面生產維?護T?PM培訓課程公開課視頻金舟軍老師好看視?頻主頁
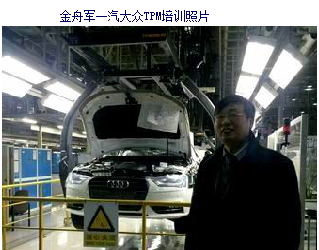
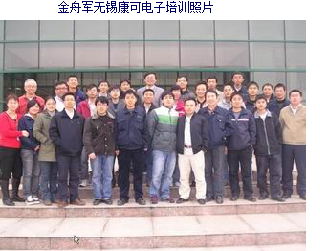
結合客戶案例的實戰型培訓 包括后服務答疑的全過程
金舟軍老師通過五大步驟結合客戶案例講解,確保學員學完全就會在工作中應用: 1 .案例網絡調研、2.案例學員預習、3. 現場案例調研、4.案例練習點評、5.售后案例答疑。
1.案例網絡調研
培訓意向一經確定,金舟軍老師就要與客戶進行網絡溝通,確定TPM實施難點,收集TPM實施資料,并就實施資料的細節進行溝通,并了解客戶學習TPM的目的。
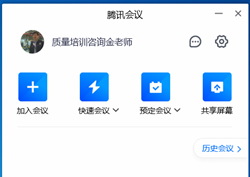
2.學員案例預習
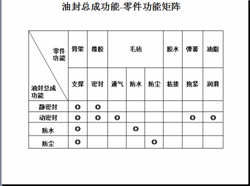
3. 現場案例調研
金舟軍老師根據TPM實施中的難點,事先為學員出TPM的預習題,幫助學員提前思考怎樣解決實施案例的難點,同時也預習課堂講解的知識。
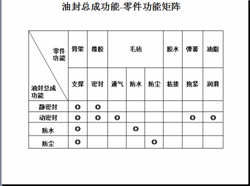
3. 現場案例調研
培訓前一天,金舟軍老師會到客戶現場進行一天的現場調研,查找客戶TPM實施V情況,并為課堂針對客戶實施TPM中的問題講解做準備。
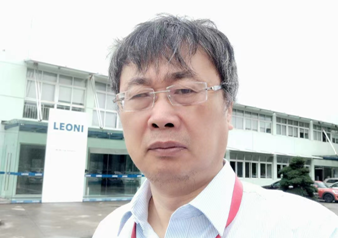
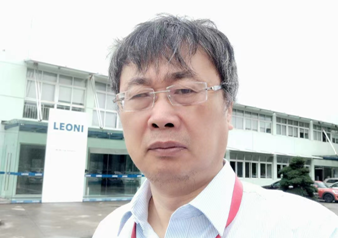
4.案例練習點評

5.售后案例答疑
培訓完成后一年之內,如果客戶在實施TPM過程中有什么問題,可以為客戶組織騰訊會議的在線答疑至少三次。
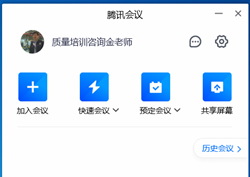
根據案例實施中的難點問題,每天培訓約有五十分鐘的客戶案例分組練習,每組學員的案例練習金舟軍老師都要做詳細的點評,確保學員學完全就會在工作中應用。

5.售后案例答疑
培訓完成后一年之內,如果客戶在實施TPM過程中有什么問題,可以為客戶組織騰訊會議的在線答疑至少三次。
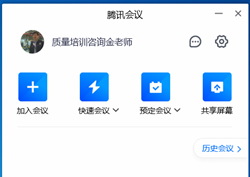
< 全面生產維護TPM培訓&設備FMEA
課程公開課大綱
一.TPM培訓目的:本課程作為生產管理實施篇,通過本課程的學習,使學員能夠理解生產管理中TPM的要求,掌握用TPM、設備SFMEA、設備SPC分析方法對進行預防性和預測性維護進行有效的策劃和實施。
二.TPM培訓對象:質量認證認證通過企業的體系管理人員、設備管理及設計人員、關鍵設備操作及維護人員。
三.TPM培訓內容:
1.設備管理
LCC壽命周期成本 金舟軍原創抄襲必告
維護Maintenance
2.故障的定義
突發型故障
老化型故障
運行不安全
3.設備管理發展歷史
BM事后維護
預防維護
糾正維護
維護預防
TPM全員生產維護
PM預測維護
案例討論-怎樣開展軍維護預防
4.設備七大損失
損失的含義
故障損失
換裝和調試損失
空閑和暫停損失
減速損失
啟動損失
質量缺陷和返工+變差損失
工裝損失
案例討論-怎樣減少減速損失
5.OEE設備綜合效率
OverallEquipmentEffectiveness
時間開動率
性能開動率
合格品率 金舟軍原創抄襲必告
完全有效生產率
案例討論-性能開動率與哪些損失有關
6.MTBF平均故障時間
平均故障壽命MTTF
部件壽命指數分布
MTBF分析的作用
案例討論-MTBF分析有哪些作用
7.設備能力指數Cmk
設備能力研究時機
設備能力指數條件
計算Cmk流程
案例討論-計算一個設備的Cmk
8.設備控制措施
故障發生的狀態及原因
預防性維護和預測性維護定義
預防維護
設備周期性計劃維修
計劃維護
基于產品要求制定周期維護計劃
日常點檢
潤滑維護
機械設備換油及潤滑保養記錄表
定期檢查
案例討論-怎樣確定周期維護計劃的舟周期
9.預測性維護
故障概率與MTBF
預測性維護技術手段
預測性維護實施方法和實例
預測性維護實施流程
磨損分析、電路回路分析、溫升分析、熱相分析、振動分析等案例。
案例討論-怎樣確定周期維護計劃的周期
10設備防錯裝置
防錯=自働化 金舟軍原創抄襲必告
自働化的特征
案例討論-確定某一設備的自働化
11.零故障5項對策
整備基本條件
遵守使用條件
使老化復原
改善設計缺陷
提高技能
案例討論-改善某一設備的設計缺陷
12.TPM全員生產維護
TPM的概念
TPM的目標
TPM的基本理念
TPM八大支柱
13.TPM的前提-5S活動
5S定義
5S之間的關系
14.自主維護
自主維護培訓
自主維護觀念形成
自主維護的范圍
15.自主維護三個活動
測定老化階段
恢復老化階段
點檢三個方面
作業前點檢
作業中點檢
作業后點檢
案例討論-完成一個點檢表
16.設備目視管理
目視管理適用范圍
設備儀表標識
案例討論-某一設備的目視管理
17.自主維護活動七步驟
初期清掃
問題根源的攻關對策
編制自主維護暫定標準
總點檢
自主點檢
整理、整頓、標準化
自主管理的徹底化
18.個別改善FocusedImprovement
個別改善流程
成立改善小組
選定改善主題 金舟軍原創抄襲必告
制定改善措施
措施實施與確認
標準化并展開
19.計劃維護
計劃維護的主要活動
大中小修理
保養基準書示例
20.設備備件管理
備件管理目標
備件管理的工作內容
21.教育和培訓
提案改善活動
提案改善的指標
建立單點教材
22.設備早期管理
維護預防
設備早期管理
Machine-Quality分析
23.部門間的效率化TPM
安全,健康和環保
24.福特MachineryFMEA
設備功能結構樹、工藝過程FMEA、設備故障樹分析FTA
設備SFMEA
設備FMEA的目的
設備FMEA的益處
功能和性能要求
潛在失效模式
硬件方法
潛在失效模式的后果
失效的潛在起因/機理 金舟軍原創抄襲必告
MFMEA頻度評價金準則
現行過程控制
MFMEA探測度的評價準則
風險順序數(RPN)
建議的措施
建議的措施責任
措施的結果
四.TPM培訓課程學時每天6.5小時共三天
設備管理
設備生命周期-設備誕生階段和誕生后階段。
全部階段的廣義設備管理:指設備的設計、制造、使用、維護、被廢棄階段。
誕生后階段的俠義設備管理:指設備誕生后的階段的設備維護管理。
LCC壽命周期成本LifeCycleCost產品生命周期的3個階段
設備研究發展階段:研究、開發時期決定了大部設備生命周期成本。
設備制造時期:制造時期對改變整體設備的成本的影響力沒有研究開發時期大。
設備運行、維護:不合格的設備設計,將會花費較高的維護、運行成本。
維護Maintenance
維護設備功能和性能的全部活動,包括預防性維護和預測性維護。
故障的定義
故障是設備失去其規定的功能和性能
突發型故障
故障導致設備不能工作。
老化型故障
故障導致設備性能降低。
故障導致設備功能降低,設備精度老化導致
產品質量缺陷。
運行不安全。
BM事后維護BreakdownMaintenance
1951年前,只是使用設備,一般不對設備進行維護,直到設備出現故障才進行維修。
1.修理查找故障原因,針對設備故障進行修理并采取措施;檢查相關零件,防止故障擴散。
2.更換正確裝配調試更換零件,并注意相關件。換下的零件修理或報廢。
預防維護PreventativeMaintenance
1951年,美國提出預防維護概念。通過對周期性故障的維護計劃,預防故障的發生,延長設備使用壽命。預防維護
包括三個方面活動:
1.設備的日常清潔,檢查和潤滑維護;
2.對設備周期性檢查,及時掌握設備老化狀況;
3.對設備老化采取的維護。
糾正維護CorrectiveMaintenance
找設備薄弱部位對其進行改進,減少故障的發生,或很容易對故障進行檢查和修復。
糾正維護由維修人員和操作人員共同參與:
1.記錄日常檢查結果和故障的詳細情況;
2.針對故障和故障發生源改進。
維護預防MaintenancePrevention
1960年開始,進入了維護預防時代。應用設備FMEA從設備的設計就開始對設備進行控制,其最終目的是實現無故障的發生和方便的日常維護.
維修人員和操作人員必須對設備的運行和維護情況進行完整的記錄,從而幫助設計人員對設備的改進。
TPM全員生產維護時代TotalProductiveMaintenance
1971年,日本導入了TPM的概念。在維護預防時代,設備的維護主要由設備專業人員進行。全員生產維護要求所有員工都對設備維護負責,強調全員參與。
PM預測維護PredictiveMaintenance
20世紀80年代之后,出現了預測維護的概念。預測維護是預測設備及其零件出現故障的原因、時段,然后采取針對性維護。
全面生產經營系統TotalProductiveManagementSystem
TPM不僅是追求設備的極限效率,而且要經由此培養出企業抵抗惡劣經營環境的體質。TPM是全面“預見管理體制”,
即TotalPredictiveManagement,一種超越現狀、邁向全面、整體的經營改革。
設備管理杠桿
應用設備FMEA從設備的設計就開始對設備進行控制的維護預防,其最終目的是實現無故障的發生和方便的日常維護。
損失的含義
損失是當前狀況與理想狀態之間的差距。認識損失存在,構筑理想狀態,尋找縮短或消除差距的改善措施。
設備管理七大損失
1.故障/損失
故障可分為功能停機型故障和功能下降型故障兩大類。
故障損失是阻礙效率的最大原因。
2.換裝和調試損失
設備從生產前一種產品,然后中止,到生產出下一種產品為止,這其中的準備、調整階段的停機就是準備、調整損失。
其中主要的是“調整時間”。
3.空閑和暫停損失
空閑和暫停損失是指由于而停頓或機器空閑時發生短暫停頓而產生這種損失。例如,有些工件阻塞了滑槽頂端,導致了設備空閑;因生產了有缺陷產品,傳感器報警而關閉了設備。很明顯,這種停頓有別于故障停工,因為除去阻塞的工件和重新啟動設備即可恢復生產。
4.減速損失
減速損失是指設計速度與實際速度的差別。速度損失對設備效率的發揮產生了較大障礙。
設備實際速度低于設計速度或理想速度的原因是多種多樣的,如機械問題和質量缺陷,歷史問題或者設備超負荷等。
5.啟動損失
啟動損失是在長時間仃產(節假日、兩班之間)后開始生產的初期階段(從設備啟動到穩定生產)產生的產量或返工、報廢損失。這些損失的數量因工序狀態的穩定性,設備、夾具和模具的維護水平,操作技能的熟練程度等的不同而異。
這項損失較大,而且是潛在的。在實際生產中,通常會不加鑒別地認為產生開工損失是不可避免的,因此很少加以消除。
6.質量缺陷和返工
質量損失是指由于設備故障引起的生產過程中的質量返工、返修和報廢損失,通常,異常原因很容易重調設備至正常狀態來消除,這些異常原因包括缺陷數的突然增加或其它明顯的現象。而普通原因難于發現,需SPC應用。
7.工裝損失
工裝損失是由于工裝失效、破損、退化和磨損引起的(時間、質量)損失,如切割工具、夾具、焊接器具和沖壓模等。